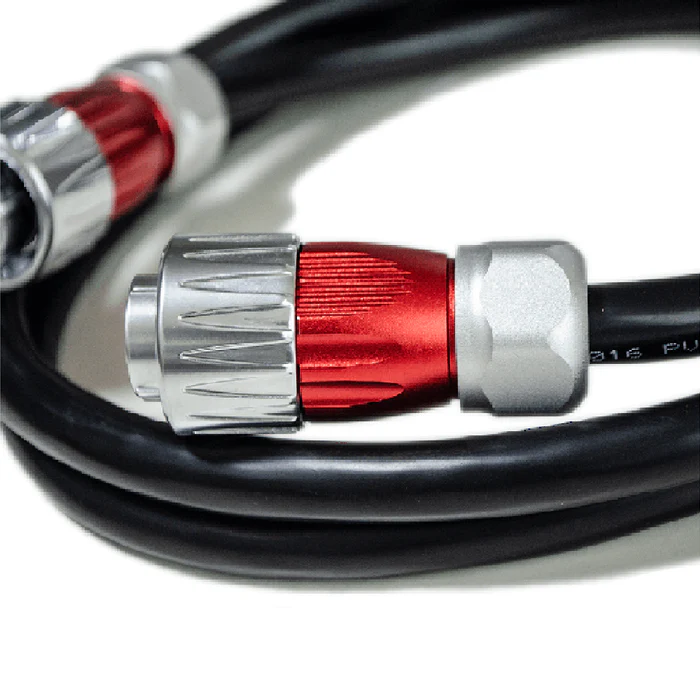
Orders & Worldwide
Orders & Worldwide
Adopting robotic automation can significantly boost productivity, quality, and competitiveness for manufacturers. However, choosing the right industrial robot for your needs requires careful consideration.
This buying guide covers the key features and capabilities to evaluate when selecting an industrial robot.
The main selection criterion for an industrial robot is its field of application. In short, what can it do for you? Thus, depending on the robot’s ultimate task you want it to fulfil, one can evaluate the whole production process in order to make up one's mind.
In the industrial robot market, there are five main types of robots one can choose from: articulated, SCARA, parallel/delta, cartesian/grantry, and collaborative/cobot.
The physical structure and layout of an industrial robot determines its appropriate applications and what it can do. The most common five types of robots' configurations are listed as follows:
It is a multi-jointed arm robots suitable for repetitive picking and placing. It has high maximum load and nice reach our range.
It is good at carrying out paint application and with high number of axes as well as high degree of flexibility and freedom (4 to 7 DOF) to reach any position and orientation in spite of obstacles. However, they are relatively expensive in cost than other types of robots plus it is not easy to program them.
This type of robot can mainly move on linear axes and are optimized for transportation and palletizing. They are easily to be programmed and are best for repetitive tasks, such as unloading machines, pick-and-place operations for injection modelling machines.
They have good precision and high level of positioning accuracy. Although they are not as flexible as articulated robot, they are low in cost.
They are robots with selective compliance arm with rigid joints which is ideal for assembly and handling. They can work along vertical axes with rotation flexibility.
Generally speaking, they function quite similarly with cartesian robots but are able to proceed tasks much faster and with higher flexibility than the former.
With the advantage of moving the Z axis to carry out vertical operations and four degrees of freedom, it can do more complex tasks than cartesian machine but at the same time still considered to be simple and not costly at all. They are more precise than the articulated robots at simpler task and can have more functionalities and flexibilities than cartesian.
These Robots are with concurrent joints that are good at providing speed and delicate precision for pick-and-place work. Delta robots, also known as Spider robots, are the most common kind within the parallel robots type.
They have a parallel configuration consisting of parallelogram joints linked to a common platform. This structure allows them to perform delicate and precise motions which are ideal for assembly, packaging, and pick-and-place tasks involving lightweight objects ranging from 10 grams to 1 kilogram.
With their dynamic movements, they are commonly used in food and pharmaceutical packaging, as well as electronics production that requires dexterous handling of small items.
They are compact, safe robots capable of working alongside humans and indeed have revolutionised the industrial world.
Since they are designed to safely work alongside humans without protective barriers, cobots utilize force control, touch sensitivity, vision systems, and anti-collision technologies to constantly monitor their surroundings and synchronize movements with operators, avoiding accidents in shared workspaces.
The benefits of cobots include low integration costs, flexible deployment, and intuitive programming enabled by their learning capabilities. However, their limitations in payload capacity and operating speed compared to traditional industrial robots make them not cost-effective enough in industrial production lines.
Owing to their safety features and adaptability, cobots are gaining popularity in sectors like automotive manufacturing for inspection and assembly tasks as well as medical fields like surgery where precision and human-robot coordination are vital.
As collaborative technology continues advancing, cobots promise to enable new human-machine workflows across industrial, medical and service applications.
The devices at the end of the robot arm that grasp, grip or handle parts are called end effectors. Common end effectors include:
Grippers - Mechanical claws that provide a sturdy grasp on objects.
Vacuum cups - Use suction to securely pick up material.
Magnetics - Utilize magnetic force to hold ferromagnetic materials.
Adhesives - Sticky tapes and gels temporarily attach to parts.
Select end effectors suitable for the shape, size and material properties of the objects handled by the robot.
The robot’s computerized control system handles programming, motion control and sensor integration for precise positioning and movement. Evaluate:
Ease of programming - From simple teaching pendants to intuitive graphical interfaces.
Autonomy - Capability to operate independently without intervention.
Vision systems - Built-in object recognition for accuracy and quality control.
Artificial intelligence - Abilities like machine learning that enable adaptability.
Interoperability - Communication and data exchange with other devices.
Key specifications like payload, precision, speed, and mobility determine suitable applications. Other factors include safety compliance, power requirements, and rated operating duty cycles.
Each type of these robots has its own strengths and advantages as well as constraints such as the number of axes, maximum load (called payload) and range . . . etc that by basing those criteria, you will be able to refine your choice.
One can match the robot configuration to one's desired and specific production tasks and workflow environment. Carefully assess your workflow needs and production environment constraints before investing in an expensive industrial robot.
Partnering with an experienced automation integrator can help identify the ideal robot configuration, capabilities, and specifications tailored to your application requirements and facilities. Investing in the right robotics solution will lead to long-term improvements in manufacturing agility, efficiency and global competitiveness.
{"one"=>"Wählen Sie 2 oder 3 Artikel zum Vergleichen aus", "other"=>"{{ count }} von 3 Elementen ausgewählt"}
Wählen Sie das erste zu vergleichende Element aus
Wählen Sie das zweite zu vergleichende Element aus
Wählen Sie das dritte Element zum Vergleichen aus
Einen Kommentar hinterlassen