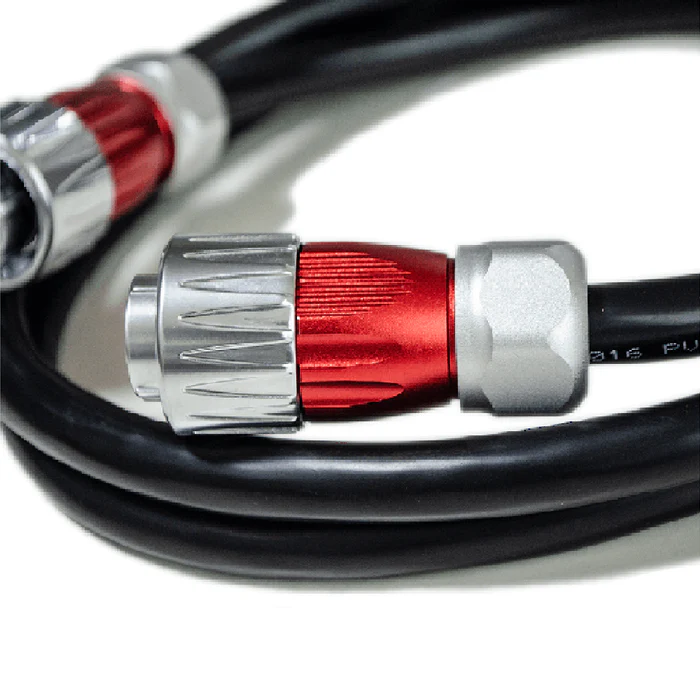
Orders & Worldwide
Orders & Worldwide
Transitioning to Industry 4.0 and automating production processes has led many businesses to consider investing in industrial robots. Before making a purchase, it's crucial to understand several key factors.
First, determine the specific task for your robot. This is the primary factor in selecting the right type of robot. If you need a compact robot for pick-and-place operations, a SCARA robot might be ideal. For high-speed placement of small items, a Delta robot is often the best choice. If you envision the robot working alongside human workers, a collaborative robot would be a suitable option.
This article focuses on industrial robots, which are versatile machines capable of performing a wide range of tasks, from material handling to machine tending, welding, and cutting. Today, industrial robot manufacturers offer a variety of models designed for various applications. Your primary task is to determine what you want your robot to do and then select the appropriate model from the numerous options available.
Key Factors to Consider When Selecting an Industrial Robot:
Payload: The payload is the maximum weight a robot can carry while operating. When calculating the payload, consider both the weight of the part and the weight of the robot's end-effector (gripper).
Degrees of Freedom (Axes): The number of axes a robot has determines its range of motion. For simple tasks like picking and placing parts between conveyors, a 4-axis robot may suffice. If the robot needs to work in a confined space and requires twisting and turning motions, a 6-axis or 7-axis robot would be a better choice. The number of axes typically depends on the specific application. Note that having more axes doesn't always equate to greater flexibility. In fact, if you only need four axes for a task and have a six-axis robot, you'll still need to program all six axes. However, having extra axes can be beneficial if you anticipate using the robot for future applications.
Robot manufacturers often use slightly different naming conventions for axes or joints. Generally, the joint closest to the robot's base is labeled J1, followed by J2, J3, J4, and so on, up to the wrist. Some manufacturers, like Yaskawa Motoman, use letters to designate axes.
Maximum Reach: When selecting a robot, consider the maximum distance the robot needs to reach. In addition to payload, you should also pay attention to the robot's maximum reach. Every manufacturer provides the robot's reach specifications, which you can use to determine if it meets your application requirements. The maximum vertical reach refers to the distance between the lowest point the robot's wrist can reach (usually below the robot's base) and the highest point. The maximum horizontal reach is the distance between the farthest point the robot's wrist can reach horizontally and the centerline of the robot's base. You should also consider the maximum working range, which is measured in degrees. These specifications can vary significantly between different robots and may limit certain applications.
Repeatability: The choice of repeatability depends on the application. Repeatability is the precision or variation with which a robot can return to the same position after each cycle. Typically, robots can achieve a repeatability of 0.5 mm or better. For applications like circuit board manufacturing, extremely high repeatability is required. If the application doesn't demand high precision, the robot's repeatability can be lower. Repeatability is usually expressed as a plus or minus value in 2D. In reality, since robots are not linear, they can reach any position within a tolerance radius.
Speed: The required speed varies depending on the application and the time needed to complete the task. Specifications typically provide the maximum speed, but the actual speed of the robot can vary between 0 and the maximum speed. Speed is usually measured in degrees per second. Some robot manufacturers also provide the maximum acceleration.
Robot Weight: The weight of the robot is an important factor when designing the robot cell. If the industrial robot needs to be mounted on a custom workstation or track, you need to know its weight to design the appropriate support.
Braking and Inertia: Robot manufacturers typically provide information about the braking system. Some robots provide braking information for all axes. To ensure accurate and repeatable positioning within the workspace, you need a sufficient number of brakes. The inertia of specific parts of the robot can be obtained from the manufacturer. This is crucial for robot safety. You should also pay attention to the allowable torque of each axis. For example, if your application requires a certain amount of torque, you need to check if the axis's allowable torque can meet the requirement. If not, the robot may fail due to overload.
Protection Rating: The required protection rating depends on the application environment. Robots working with food products, laboratory instruments, medical devices, or in flammable environments require different protection ratings. This is an international standard, and you need to determine the required protection rating based on the actual application or local regulations. Some manufacturers offer different protection ratings for the same robot model to accommodate various working environments.
Key Performance Parameters of Industrial Robots:
Environmental Requirements for Industrial Robots:
0 de 3 itens selecionados
Selecione o primeiro item para comparar
Selecione o segundo item para comparar
Selecione o terceiro item para comparar
Deixe um comentário