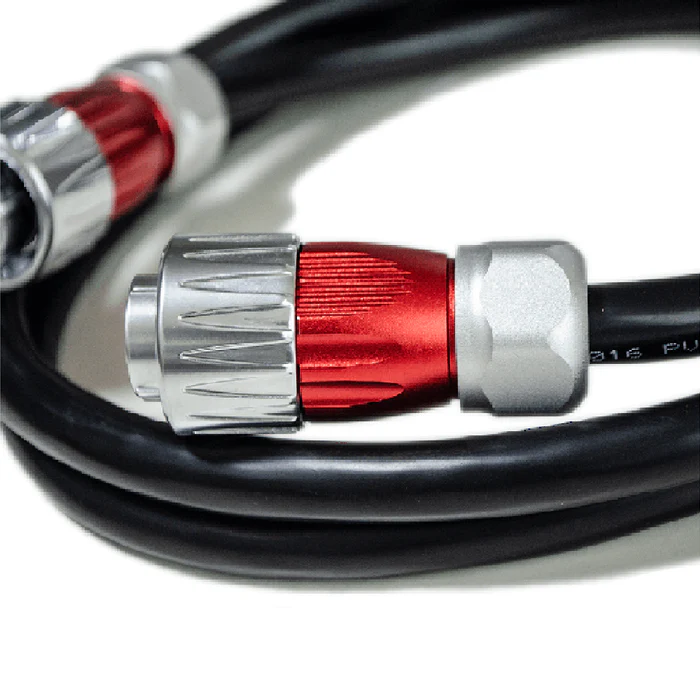
Orders & Worldwide
Orders & Worldwide
Sourcing and procuring cost-effective robotic spare parts are vital for maintaining efficient and reliable robotic systems while minimizing expenses. As automation technology becomes increasingly common across industries, it is crucial to establish streamlined processes to procure spare parts. Organizations can optimize their procurement practices and save money by using effective strategies and sourcing channels.
The following strategies can help organizations maximize the performance of their robotic systems while minimizing costs. Furthermore, this will give your company a competitive advantage in the dynamic world of robotic automation. Let's dive into the actionable strategies to empower you to achieve substantial cost savings in your sourcing and procurement process.
Cost Effective Strategies for Sourcing and Procuring Robotic Spare Parts
Assessing Spare Parts Requirements is crucial in implementing a cost-effective sourcing and procurement strategy for robotic spare parts. This process involves the steps below:
1. Identifying Key Components and Spare Parts:
The first step is identifying the essential components and spare parts required for the specific robotic systems. Common parts that may require replacement over time include batteries, cables, teach pendants, grease, motors, end-effector parts, and welding consumables. Companies can ensure they are included in the procurement plan by understanding the specific spare parts needed.
2. Analyzing Frequency of Parts Replacement and Associated Costs:
Analyzing the frequency of parts replacement is essential to determine the optimal stocking levels. By reviewing historical data, maintenance records, and equipment specifications, companies can identify patterns and estimate how often certain parts need to be replaced. This analysis allows for proper planning and budgeting for spare parts procurement. Additionally, assessing associated costs provides insights into the financial impact of part replacements and helps identify cost-saving opportunities.
3. Determining Criticality of Spare Parts:
Understanding the criticality of each spare part is crucial to prioritize procurement efforts. Some spare parts may require immediate availability depending on their importance to the robotic system's operation. Conversely, less critical components may have longer lead times or lower stock levels. Identifying the criticality of spare parts allows companies to allocate resources efficiently. For instance, companies can allocate budgets for necessary spare parts while reducing spending on less-needed parts.
When selecting a vendor for robotic spare parts, it is crucial to thoroughly evaluate their track record and operational strength. Look for a robotic spare parts company with a proven history of maintaining operational efficiency and meeting lead times. This indicates their ability to consistently deliver on their promises and meet customer expectations. Assess their financial stability to ensure a sustainable long-term solution and mitigate the risk of potential disruptions in the supply chain.
Furthermore, consider partnering with a spare parts vendor that can provide international support. A robotic spare supplier with a global presence can be advantageous, as they can offer localized service, maintenance, training, and financing options. This ensures that you receive comprehensive support regardless of your geographic location and facilitates smoother operations on a global scale.
Finally, prioritize vendors who value their customers. While technology and self-service options are valuable, the human element should not be underestimated. Choose a vendor that values personal interactions and provides prompt and helpful customer support. Thus, you have a reliable point of contact who can address your concerns and provide tailored solutions. Here are some robotic spare part marketplaces to help you find trusted suppliers:
Negotiation is a crucial aspect of sourcing and procuring robotic spare parts. To ensure cost-effectiveness, developing a negotiation strategy with the supplier is essential. Here are some points to consider:
Develop a Negotiation Strategy: Establish a clear negotiation strategy focusing on securing competitive spare parts pricing. Identify your goals, desired pricing range, and key terms to negotiate with the supplier.
Explore Bulk Purchasing Options: Inquire about bulk purchasing options and discounts for volume orders. Purchasing in larger quantities can often lead to cost savings and lower per-unit prices. Explore the feasibility of consolidating orders to take advantage of these benefits.
Discuss Potential Contractual Terms:
Open the Discussion for Discounts:
By developing a negotiation strategy, you can effectively negotiate with the supplier and secure cost-effective pricing for robotic spare parts.
Buying refurbished parts can be a viable option for saving expenses when sourcing robotic spare parts. However, when considering sourcing refurbished parts, evaluating the potential cost savings and associated risks is crucial. Calculate the price difference between new and refurbished parts, taking into account any warranty coverage provided. Additionally, consider your robotic system's specific requirements and demands to ensure compatibility and reliability. By carefully assessing the cost savings and potential risks, you can determine whether purchasing refurbished parts is suitable and cost-effective for your spare parts procurement.
Several reputable companies, including EU Automation, Eurobots and KUKA, officially sell refurbished parts with good warranties. These parts undergo a thorough refurbishment process, ensuring they are fully functional. When you explore these options, you may be able to obtain high-quality components for a lower price than if you purchased them brand new. If you buy refurbished parts from reliable suppliers, you can save significantly on costs without sacrificing quality.
Effective inventory management and optimization are crucial for minimizing downtime and financial losses. Maintaining an adequate stock of spare parts for robots helps prevent unplanned or prolonged downtime. As a result, it decreased productivity and caused significant financial losses. Optimizing spare parts holding involves analyzing usage patterns, forecasting demand, and assessing criticality. By understanding the frequency and criticality of part replacements, companies can determine the optimal quantity of each spare part in stock. This optimization balances carrying excess inventory, tying up capital, and the risk of insufficient parts causing prolonged downtime.
Implementing advanced techniques like just-in-time (JIT) inventory further optimizes inventory levels. This approach minimizes carrying costs and the risk of obsolete inventory while efficiently supplying spare parts when needed. Companies can also leverage inventory management software or systems that streamline the tracking, monitoring, and reordering spare parts. These tools provide real-time visibility into inventory levels, automate reorder processes, and facilitate accurate demand forecasting. They enhance inventory control, reduce manual errors, and enable proactive maintenance planning.
Learning and knowledge sharing are essential for improving robotic spare parts procurement practices and reducing costs. To reduce spending, educate your team on best procurement practices. Provide training and resources focused on cost-effective strategies, negotiation skills, and supplier management. You can save significant amounts of money by equipping your team with knowledge. Cost-effective procurement also involves collaboration. Increase collaboration with other departments and external organizations to reduce procurement costs. Working together allows you to benefit from economies of scale, pool resources, and negotiate better supplier contracts.
Knowledge-sharing platforms and databases are crucial for capturing lessons learned, best practices, and success stories. By creating a centralized platform, procurement professionals can exchange insights, share experiences, and improve cost-effective solutions continuously. All of these things result in cost savings by reducing unnecessary spending. These strategies will boost your organization's efficiency, drive continuous improvement, and maximize procurement value.
Continuous Improvement and Evaluation are crucial for maintaining cost-effective sourcing and procurement of robot spare parts. Monitor and evaluate the effectiveness of the cost-effective strategies you have implemented. Track key metrics such as cost savings, procurement cycle time, and supplier performance. Assessing the results of your strategy will help you identify areas for improvement.
You should also regularly review your sourcing and procurement processes to keep them up-to-date with changing market trends. Over time, robots and robot parts may change, and the demand for specific spare parts may also vary. Stay informed about technological advancements, industry trends, and market demands. This helps prevent inventory and stockouts by sourcing the right parts at the right time.
The process can often be daunting and time-consuming when sourcing cost-effective spare parts for your robotic systems. However, with inRobots, you can trust that the journey will be hassle-free and efficient. inRobots is a global platform dedicated to helping companies succeed with automation. With their extensive worldwide directory of major robotics companies, inRobots provides a comprehensive resource for finding the exact type of robotic component you need, perfectly suited for your specific application.
inRobots understand the importance of optimizing procurement costs while maintaining the quality and reliability of the spare parts. By relying on inRobots, you can streamline the sourcing process, minimize expenses, and achieve significant savings for your organization. Whether you require critical components or routine replacement parts, inRobots's directory has what you're looking for.
Choose inRobots as your go-to resource for cost-effective robotic spare parts sourcing, and experience a streamlined and successful procurement process that enhances the performance and longevity of your robotic systems.
{"one"=>"Selecione 2 ou 3 itens para comparar", "other"=>"{{ count }} de 3 itens selecionados"}
Selecione o primeiro item para comparar
Selecione o segundo item para comparar
Selecione o terceiro item para comparar
Deixe um comentário